LEAN MANAGEMENT 4.0
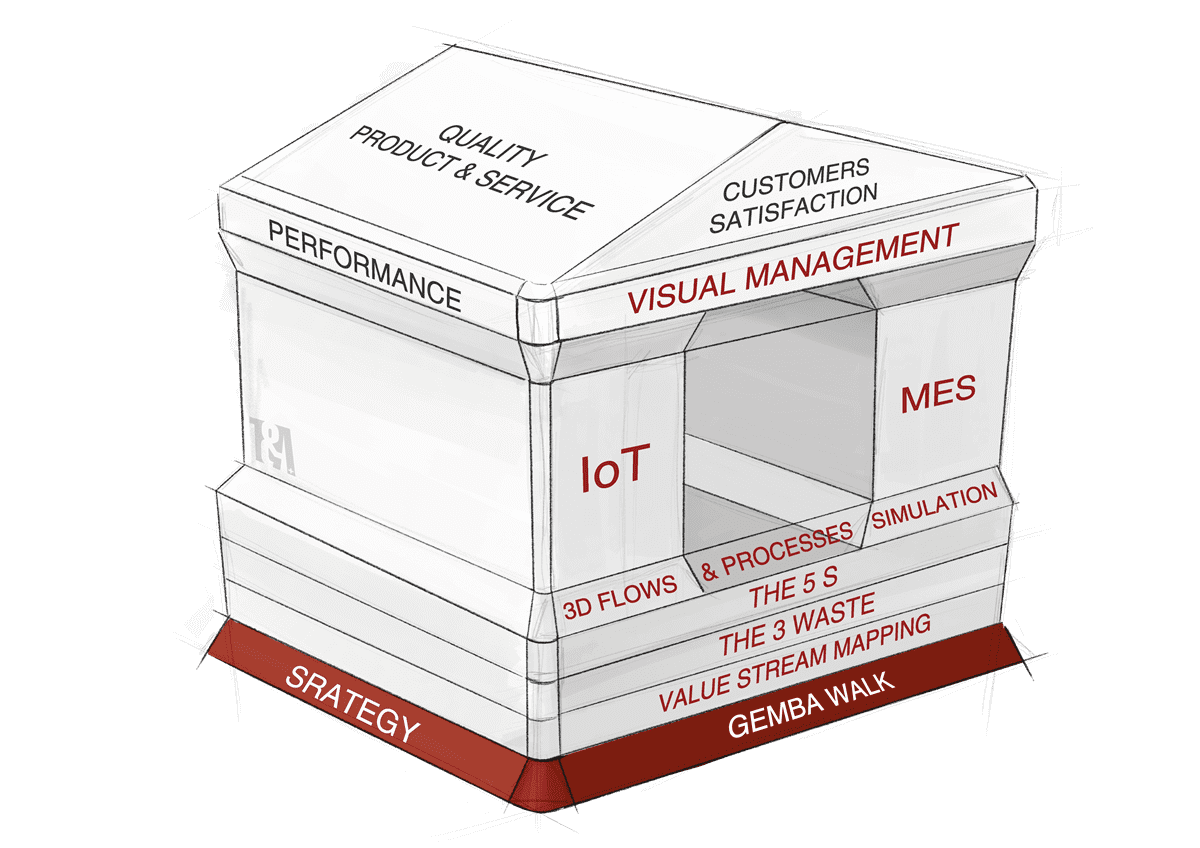
À LA RECHERCHE DE L'EXCELLENCE
Le Lean est une philosophie d'entreprise, née dans les années 50 au Japon chez Toyota, visant à améliorer la performance des processus grâce à quelques outils, des méthodes et des bonnes pratiques accompagnés de beaucoup de bon sens et de rigueur. Au cours des ans, il est le fruit d'innombrables retours d'expériences pratiques qui ont donné naissance à des méthodologies et à un cadre de référence. C'est une approche qui est dédiée principalement au managment.
HISTORIQUE DU LEAN
De tout temps, l'Homme a cherché à améliorer sa qualité de vie en accroissant les performances, dans un premier temps, de ses outils de travail manuels, puis des systèmes mécaniques - Révolution industrielle 1.0, des systèmes électriques - Révolution industrielle 2.0, des systèmes électroniques et informatiques - Révolution industrielle 3.0 et actuellement des cybersystèmes connectés - Révolution industrielle 4.0.
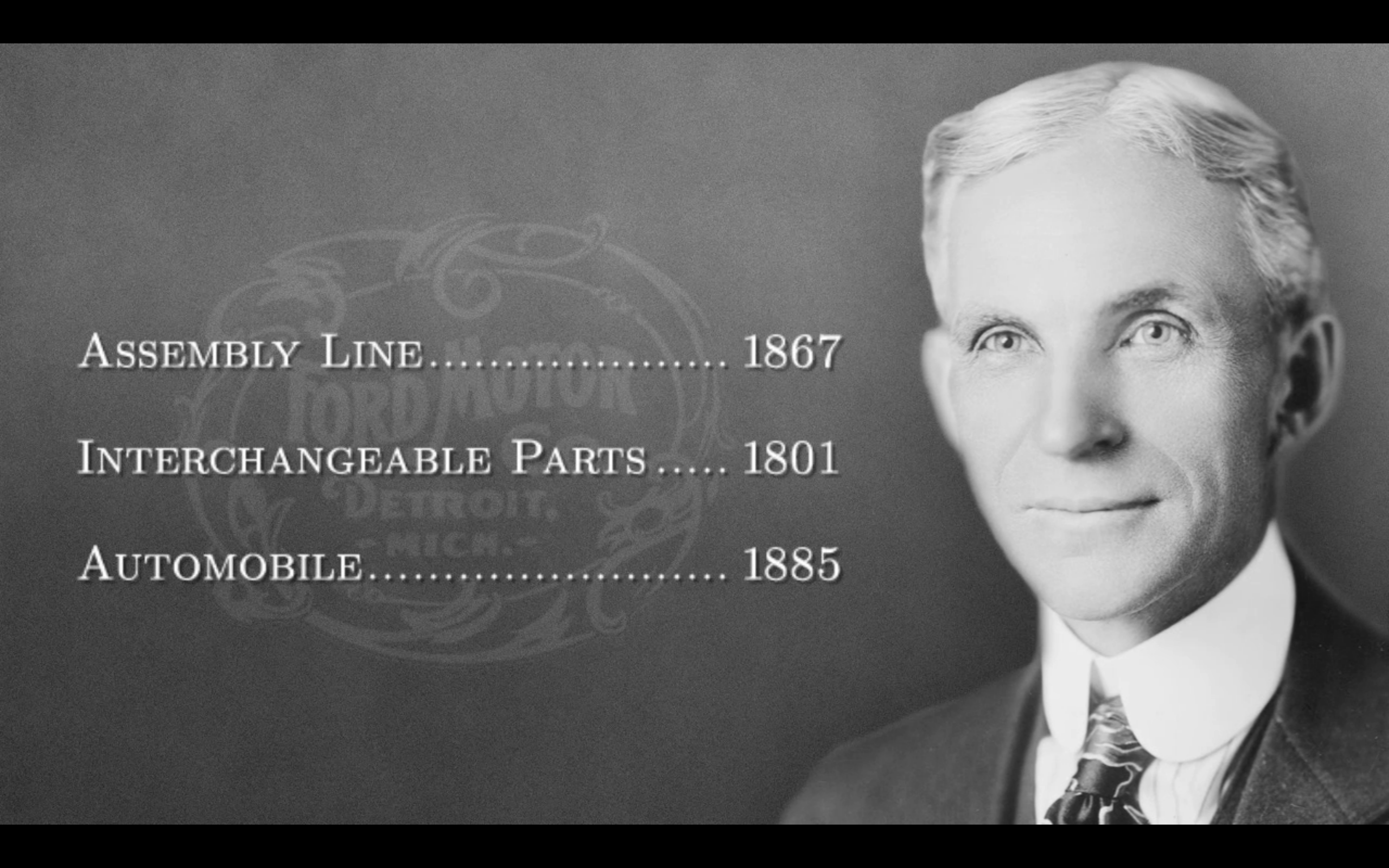
"Je construirai une voiture abordable pour tout le monde", a proclamé Ford en annonçant la naissance du modèle T en octobre 1908.
En 1913, Ford a lancé la première chaîne de montage mobile pour la production de masse de l'automobile. Cette nouvelle technique a réduit le temps pour construire une voiture, passant de 12 heures à 2,5 heures, ce qui a à son tour abaissé le coût du modèle T de 850 $ en 1908 à 310 $ en 1926.
Henry Ford a été le premier a intégrer un processus de production global en créant des chaines de production avec un flux continu de pièces.
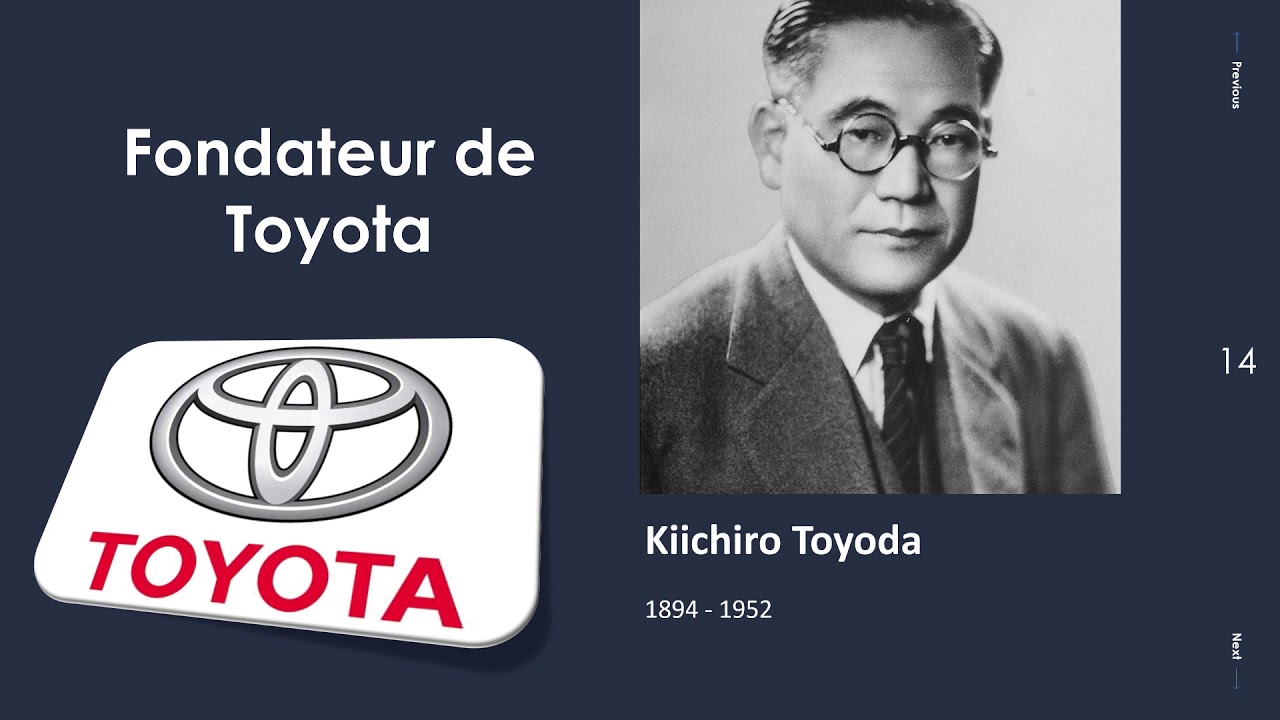
Dans les années 1950, l'entreprise japonaise Toyota est 8 fois moins performante (productif) que ses concurrents américains. Elle veut relever le défi, Kiichiro Toyoda, fils du fondateur de Toyota, s'en remet au génie de 2 ingénieurs Taiicho Ohno et Eiji Toyoda qui ont développé un nouveau système de performance d'entreprise appelé le TPS qui est à l'origine du LEAN :
- Toyota
- Production
- System
Les principaux objectifs du TPS sont d'éviter les surcharges (muri) et incohérences (mura), et d'éliminer les gaspillages (muda). Il aura fallu près de 60 ans à Toyota pour devenir le N°1 mondial de l'automobile.
ÉVOLUTION DU LEAN
1913
Henry Ford, fondateur de Ford Automobiles, invente et implémente les prémices de Lean, à savoir: la standardisation des modèles de produits, la réduction des gaspillages en termes de mouvements et de tâches, le Juste-à-Temps au niveau de la chaîne d'approvisionnement.
1924
Sakichi Toyoda, fondateur d'une usine de métiers à tisser, invente le concept de l'autonomie
1937
Kiichiro Toyoda, fils de Sakichi Toyoda, fondateur de Toyota Automobiles, développe des méthodes basées sur la réduction des gaspillages.
1938
Le concept JAT - Juste à temps naît au sein de Toyota
1940
Kaoru Ishikawa invente le diagramme en arrête de poisson comme méthode de résolution de problème
1940
Toyota invente le TWI - Training Within Industry ou formation des collaborateurs et partage des connaissances sur le terrain
1949
Taiichi Ohno développe le concept de l'élimination des gaspillages (muda-mura-muri)
1951
Taiichi Ohno améliore le sytème TPS en intégrant : le contrôle visuel, le feedback des collaborateurs, le TWI, la réduction de la taille de lots et le Kanban
1965
Toyota reçoit le prix Deming pour la Qualité
1975
Le TPS est mature et inclu dorénavant le JAT, le Kanban, le TQM et le Kaizen
1986
Motorola invente le Six Sigma
1988
Taiichi Ohno publie le TPS
1988
Les méthodes résultantes du TPS ont été étudiées à partir du milieu du 20e siècle et surnommées «LEAN» par John Krafcik
1988
Norman Bodek et Vern Buehler créent le prix de l'Excellence Opérationnelle (Prix Shingo)
1988
Création de l'EFQM (European Foundation for Quality Management) créant une référence européenne pour l'Excellence Opérationnelle
1990
James P. Womack, Daniel Roos et Daniel T. Jones publient : "The Machine that changed the world" après 5 années d'études
2001
Jeffrey Liker publie les "14 principes qui feront la réussite de votre entreprise". Ces 14 principes sont devenus communément une référence.
2007
Toyota devient le premier constructeur automobile mondial
QU'EST-CE QUE LE LEAN
Le LEAN est une approche systémique pour concevoir et améliorer les processus en visant un état idéal centré sur la satisfaction du client par l'implication de l'ensemble des collaborateurs.
Le LEAN est un système visant à générer une valeur ajoutée maximale, au moindre coût et au plus vite, cela en employant les ressources juste nécessaires pour fournir aux clients ce qui fait de la valeur à leurs yeux.
Le Lean orienté plus opérationnel peut aussi se définir comme une observation structurée dans un cadre de référence. l'observation doit mener à comprendre comment les activités sont interconnectées entre elles, de quelles natures sont leurs relations et comment permettre l'écoulement d'un flux idéal.
LES 14 PRINCIPES DE MANAGEMENT DE DEMING (1986)
Ces principes sont les fondements de la transformation de l'industrie
William Edwards Deming, maître du Management de la Qualité Totale :
1. Gardez le cap sur votre mission en améliorant constamment les produits et les services. Le but d'une entreprise est d'être compétitive, d'attirer des clients et de donner du travail.
2. Adoptez la nouvelle philosophie. Nous sommes dans un nouvel âge économique. Les dirigeants occidentaux doivent s'informer de leurs nouvelles responsabilités et conduire le changement.
3. Faites en sorte que la Qualité des produits ne demande qu'un minimum de contrôles et de vérifications. Intégrez la Qualité au produit dès la conception.
4. Abandonnez la règle des achats au plus bas prix. Cherchez plutôt à réduire le coût total. Réduisez au minimum le nombre de fournisseurs par article, en établissant avec eux des relations à long terme de loyauté et de confiance.
5. Améliorez constamment tous les processus de planification, de production et de service, ce qui entraînera une réduction des coûts
6. Instituez une formation professionnelle permanente.
7. Instituez le leadership, nouvelle manière pour chacun d'exercer son autorité. Le but du leadership est d'aider les hommes et les machines à mieux travailler. Révisez la façon de commander.
8. Chassez la crainte, afin que tout le monde puisse contribuer au succès de l'entreprise.
9. Détruisez les barrières entre les services. Le travail dans un esprit d'équipe évitera que des problèmes apparaissent au cours de l'élaboration et de l'utilisation des produits.
10. Supprimez les exhortations et les formules qui demandent aux employés d'atteindre le zéro défaut pour augmenter la productivité. Elles ne font que créer des situations conflictuelles.
11. Supprimez les quotas de production, ainsi que toutes les formes de management par objectifs. Ces méthodes seront remplacées par le leadership.
12. Supprimez les obstacles qui empêchent les employés, les ingénieurs et les cadres d'être fiers de leur travail, ce qui implique l'abolition du salaire au mérite et du management par objectifs.
13. Instituez un programme énergique d'éducation et d'amélioration personnelle
14. Mobilisez tout le personnel de l'entreprise pour accomplir la transformation
LES 5 PRINCIPES DE WOMACK (1990)
Ce sont les principes initiateurs du Lean qui sont des formulations synthétiques et conceptuels.
James P. Womack et Daniel T. Jones ont énoncés 5 principes génériques à la naissance du Lean:
1. Définir la valeur - Spécifier ce qui fait ou crée de la valeur pour le client
2. Identifier le flux de valeur
3. Créer le flux - Favoriser l'écoulement du flux
4. Tirez les flux
5. Viser la perfection
LES 14 PRINCIPES DE LIKER (2001)
Ces principes sont devenus LA référence de la définition de Lean Management
Jeffrey Liker a traduit et formulé le système TPS de Toyota en 14 principes transposables à d'autres secteurs d'activité.
1. Fondez vos décisions sur une philosophie à long terme même au détriment des objectifs financiers à court terme
2. Organisez les processus en flux pièce à pièce pour mettre à jour les problèmes
3. Utilisez des systèmes tirés pour éviter la surproduction
4. Lissez la production (heijunka)
5. Créez une culture de résolution immédiate des problèmes, de qualité du 1er coup
6. La standardisation des tâches est le fondement de l'Amélioration Continue et de la responsabilisation des employés
7. Utilisez le contrôle visuel afin qu'aucun problème ne reste caché
8. Utilisez uniquement des technologies fiables, longuement éprouvées, qui servent vos collaborateurs et vos processus
9. Formez des responsables qui connaissent parfaitement le travail, vivent la philosophie du Lean et l'enseignent aux autres
10. Formez des individus et des équipes exceptionnels qui appliquent la philosophie de votre entreprise
11. Respectez votre réseau de partenaires et de fournisseurs en les encourageant et en les aidant à progresser
12. Allez sur le terrain pour bien comprendre la situation (genchi, gembutsu)
13. Décidez en prenant le temps nécessaire, par consensus, en examinant en détail toutes les options. Appliquez rapidement vos décisions
14. Devenez une entreprise apprenante grâce à la réflexion systématique (HANSEL) et à l'amélioration continue (KAIZEN)
lean management 4.0
LEAN
OBSERVER ET ÉLIMINER LES GASPILLAGES
LEAN MANUFACTURING
ACCROÎTRE L'EFFICIENCE DES PROCESSUS DE PRODUCTION
LEAN MANAGEMENT
ACCROÎTRE L'EFFICIENCE DE L'ENTREPRISE
LEAN MANAGEMENT 4.0
ACCROÎTRE L'EFFICIENCE DE L'ENTREPRISE GRÂCE AUX TECHNOLOGIES 4.0
LEAN OFFICE 4.0
ACCROÎTRE L'EFFICIENCE DES PROCESSUS ADMINISTRATIFS GRÂCE AUX TECHNOLOGIES 4.0
INDUSTRIE 4.0
ACCROÎTRE L'EFFICIENCE ET LA COMPÉTIVITÉ DE L'ENTREPRISE GRÂCE AUX TECHNOLOGIES 4.0
RÉSULTATS attendus GRÂCE AU LEAN MANAGEMENT 4.0
DURÉE MOYENNE D'IMPLÉMENTATION
2-4 ANS
ACCROISSEMENT MINIMUM DE L'EFFICIENCE